A Place for Traditional Hand Tool Woodworking
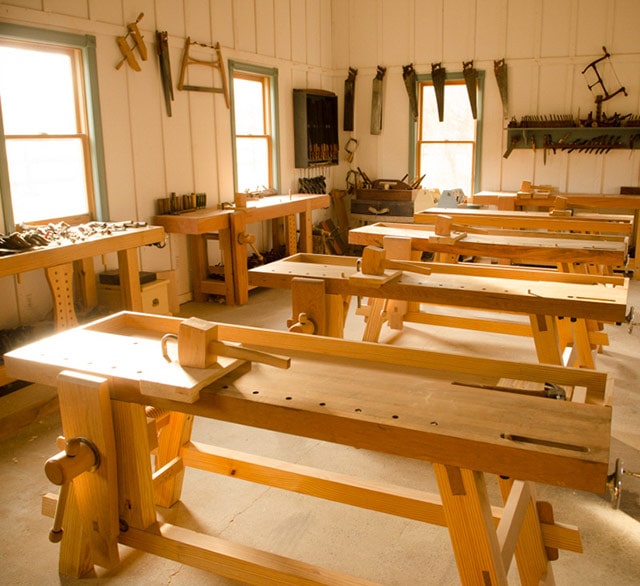
“Wood and Shop is a place for Woodworkers to Learn a Mix of Traditional Hand Tool Woodworking, with Modern Power Tool Woodworking, to Make Heirloom-quality Furniture that will Last Multiple Lifetimes.”
– Joshua Farnsworth

Wood & Shop
Wood and Shop in your inbox?
Subscribe to get Joshua's free traditional woodworking videos, articles & news:
You have Successfully Subscribed!